TRANSFORMACIÓN FÍSICA DE LA BIOMASA
- ESTUDIO DE LAS APLICACIONES DE LAS DIFERENTES FRACCIONES DE LA FITOMASA
FORESTAL.
Durante
el proyecto, se realizaron una serie de pruebas industriales y de laboratorio
para evaluar la aplicación técnica de distintos materiales procedentes
de la fitomasa forestal, como elementos densificados.
Proceso
de fabricación de elementos densificados. Fases del proceso.
ASTILLADO - MOLIENDA
Los mejores rendimientos energéticos en la fase
de molienda se obtuvieron con la corteza de pino, seguida de los restos
de corta de pino y eucalipto. En el caso de la corteza de eucalipto no
se han conseguido buenos resultados.
La molienda del material con mallas de menos
de 10 mm aumenta considerablemente el consumo energético de este proceso,
si bien la mejora en la calidad final del producto no es demasiado importante.
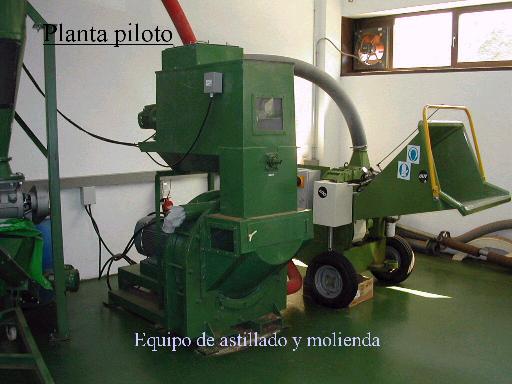
Las
distribuciones granulométricas son sensiblemente diferentes debido a la
diversa naturaleza y presentación de los productos estudiados.
PRODUCCIÓN
DE ELEMENTOS DENSIFICADOS
Una
de las posibilidades de transformación física de la biomasa, consiste
en su compactación para la obtención de productos combustibles densificados
con un alto poder calorífico, homogéneos en propiedades y dimensiones,
lo que permite la automatización de los sistemas de alimentación y control
de la combustión.
Se
pueden diferenciar dos tipos de material densificado:
- BRIQUETAS:
Durante el proceso de briquetado se generan elevadas presiones (200 Mpa/cm2),
que provocan un incremento térmico de 100 a 150º C, esta temperatura provoca
la plastificación de la lignina que actúa como elemento aglomerante de
las partículas de madera. Para que tenga lugar este proceso de autoaglomeración
es necesario que el material tenga una humedad entre 8 y e 15 % B.H. y
que el tamaño de partícula sea del orden de 0,5 a 1 cm.
- PELLETS:
Su fundamento operativo se basa en la presión ejercida por una serie de
rodillos sobre los residuos situados sobre una matriz metálica dotada
de orificios de calibre variable (0,5 a 2,5 cm). El material base debe
tener una humedad entre 8 y 15 % B.H. y un tamaño de partícula del orden
de 0,5 cm. El tamaño del pelet suele estar entre 0,5 a 2,5 cm de diámetro
y de 1 a 3 cm de longitud.
Los
materiales empleados para las pruebas fueron:
Serrín
y viruta roja.
Corteza
de pino
Corteza
de eucalipto
Restos
de corta de eucalipto
Restos
de corta de pino
Con
estos materiales se realizaron las siguientes pruebas:
1. Densificado en
planta piloto con equipo de briquetado hidráulico.
2. Densificado en
planta industrial con equipo de briquetado de pistón (350 kg/h).
3. Pelletizado en
planta industrial con equipo de pelletizado con matriz plana (2.500 kg/h).
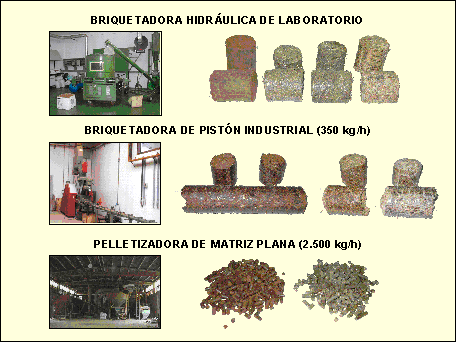
Se
realizaron pruebas con distintas granulometrías de material, distintas
humedades y con distintas mezclas de materia prima.
En
todos los casos se han conseguido productos densificados semejantes a
los que se comercializan en la actualidad. Únicamente en el caso de la
corteza de eucalipto se han encontrado dificultades técnicas que hace
difícilmente viable su aplicación en estos productos.
A
continuación se reseñan las conclusiones más significativas obtenidas
en cada fase:
COMPACTACIÓN
– DENSIFICACIÓN
-
Se han conseguido briquetar en la planta piloto todos los productos a
baja presión y temperatura, obteniéndose briquetas de calidad
y aspecto muy aceptable, si bien con menores densidades que las obtenidas
en instalaciones industriales donde se trabaja a mayor presión
y temperatura.
- La
corteza de eucalipto se densifica con dificultades y el tamaño obtenido
es sensiblemente inferior al normal. En términos económicos no resulta
rentable la densificación de corteza de eucalipto, convendría en cualquier
caso mezclarla con otros productos.
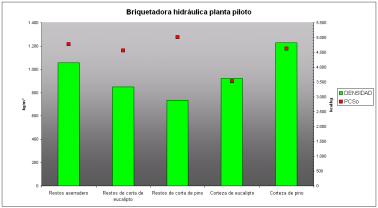
- En las pruebas de
briquetado a escala industrial se han conseguido excelentes resultados
de producción en todos los casos, si bien en el caso de corteza de eucalipto
ha sido necesario mezclar ésta con otros residuos para garantizar su dosificación
y densificación.
-
en las pruebas de pelletizado a escala industrial, se ha conseguido en
todos los casos fabricar pellets sin mayores complicaciones y se han obtenido
productos finales muy semejantes a los que se comercializan en la actualidad.
en el caso de la corteza de eucalipto ha sido totalmente imposible obtener
pellets debido a la formación de atascos en las cribas para la
clasificación del material.
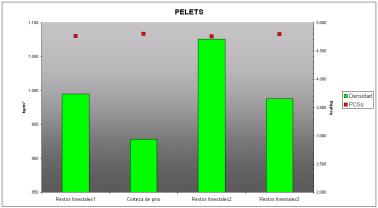
SECADO
NATURAL Y FORZADO
En
determinadas circunstancias, es necesario proceder a la deshidratación
de la biomasa. Dos son los sistemas de secado utilizados, el secado natural
y el secado forzado.
- Durante
el secado natural se aprecian 3 zonificaciones claramente definidas en
todos los casos estudiados. Una zona superficial que responde fielmente
a la influencia atmosférica, una zona interior que evoluciona de forma
diferenciada debido a la influencia de fenómenos termogenésicos de tipo
microbiológico y termoquímicos. Finalmente existe una capa de cumbrera
de poco volumen que evoluciona de forma diferente atendiendo a los cambios
ambientales y a la influencia de la zona interior.
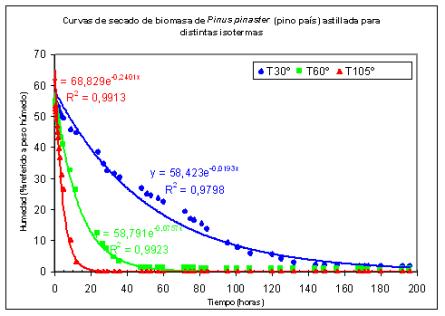
-
Se han obtenido unos ratios, para secado forzado de astilla de
eucalipto y pino con un flujo de 1.300 kg/h, de aire/madera de entre 3
y 8 kg/kg y de aire seco/madera de 0,2 kg/kg, así como de aire seco/agua
evaporada de unos 15 kg/kg. Estos datos serían básicos para el diseño
de secaderos específicos.
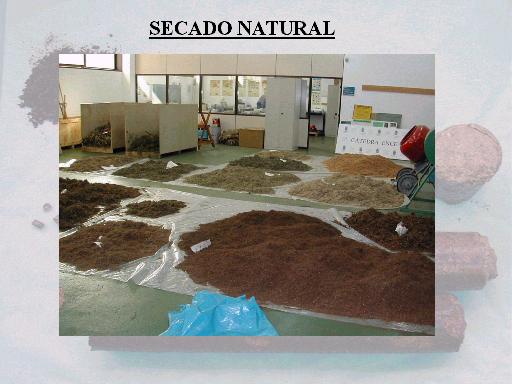
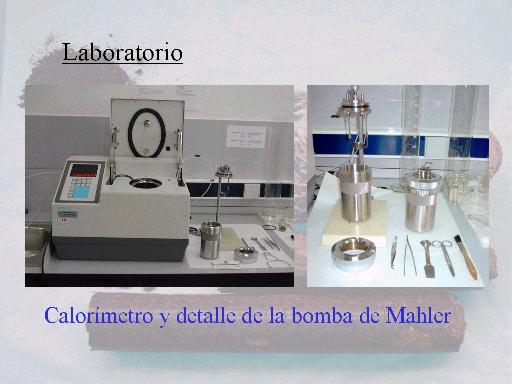
|